business performance
Product Development and Safety
All operations are concentrated in a single business niche – high-end real estate. The process has five steps:
1
Prospecting
Through the Development area, we prospect the best land, considering the location, potential for appreciation, public transport, infrastructure, and the neighborhoods in which we have a good sales history.
2
Feasibility
Once the land is identified, the Costs area analyzes the purchase conditions and the feasibility of the acquisition. Then, studies are carried out, such as topographical survey, sounding, analysis of quotas, mass study, among others.
3
Planning
The third stage is the planning of the work. A detailed study is carried out from the design of the project. In this phase, several areas of the Company operate in an integrated manner.
4
Launch
It is up to the Launch Committee (COLAN), composed of members of the executive board, to approve or not the viability of the launch.
5
Sales
After project approval, promotion and sales strategies are designed, processes ranging from setting up the stand to defining the conditions for selling the units.
Before handing over the keys, all units are thoroughly inspected. Finally, a General Installation Meeting is held and the condominium is created. We had no cases linked to health problems since our product is durable and meets all legal and regulatory requirements.
Technical Support Activities
Product Safety
The experience of over 40 years in civil construction in high-end works and our financial solidity – reflecting a responsible and efficient corporate governance, with consistent financial management, together with a mature, well-structured, and recognized business model in the market – make up the main indicators of the quality of our products.
The annual renewal of important international certifications, such as ISO 9001:2015, proves the efficiency of our management model. In the country, we have the PBQP-H:2021 certification, from the Habitat Brazilian Quality and Productivity Program, which endorses our constructive quality and the assertiveness of the search for innovation and sustainable processes.
During the construction process, we have several quality controls in place to ensure that projects are in line with our standards and, since the previous year, we have improved safety with the implementation of the above Prevention cell, which monitors all works, to ensure that the improvements developed in the Problema Zero program are correctly applied, the execution of the work is in accordance with the guidelines and technical procedures foreseen and any deviations are detected at an early stage and duly resolved.
As a result of this effort, in 2022, we had no incidents of fines, penalties or warnings for non-compliance with laws and/or voluntary codes regarding impacts on health and safety caused by products and services.
Classify the degree of importance of each maintenance for the safety of the building;
Signaling required or overdue maintenance to all responsible parties on a monthly basis; and
Avoid overlooking any maintenance that affects the safety or health of the users, such as the firefighting system, elevators, cleaning of water tanks, sewage system, etc.
Produto Fantástico
The Produto Fantástico project was born from the proposal to develop a product that could offer solution platforms for the daily problems of modern life, anticipate trends, and provide a new way of living, working and living within the enterprise itself, with all the comfort and safety.
The project focuses on seven pillars: Conception, Conceptualization, Construction Quality, Excellence Services, Safety, Convenience and Relationship. To meet all these aspirations, the developments have markets, stores, gyms and other advantages, along with the best technologies aimed at thermal, lighting, acoustic and hydro-sanitary comfort, among others.
With all these amenities, the developments become hubs for the integration of sports, work and even gastronomic areas, which add value to the development and even the surroundings. High standard projects with the Fantastic Product concept generate positive impacts, such as greater commercial development in the region, appreciation of the square meter in the regions where it is present and one of the highest profitability in the market for the customer, which also translates into good options for investors.
To make these ventures a reality, which contribute to both social and environmental aspects and well-being for the client, our internal management model allows us to define goals (financial or otherwise), measure results and evaluate processes, to guarantee a high level of satisfaction. of customers.
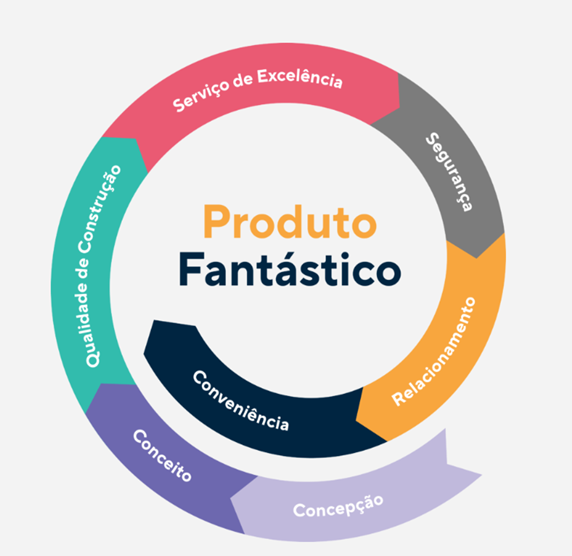